Training
Analog Drilling Rig SCR System Maintenance and Repair
When you go to an automobile mechanic, would you accept it if he were to say, “I can’t work on your Ford. I’m a BMW mechanic?” Yet in the oil patch, many electricians won’t work on a system for similar reasons: “I can’t work on that. It’s a Ross Hill® system, and I’m a Bentec ® electrician.”
At WWPS, we help to eliminate the above situation with our unique approach to SCR system training. Our classes are designed to show how the different components fit together, regardless of the manufacturer. We use real world systems to explain real world operation. We don’t concentrate on schematics or specific levels. Instead, we show the signals needed to perform any typical operation, and how those signals can be derived and applied. The student can then take these lessons into the field and apply general principals to solve a problem, regardless of the system generating the signals.
As an example of the above approach, every alternator (AC electric generator) requires an excitation voltage and current within its nameplate rating. How do you check any alternator’s excitation? How do you check the excitation voltage? How do you read the nameplate and what does it tell you? It doesn’t matter if you have an SCR-controlled source for variable DC, or an IGBT-controlled source for PWM, the level and reason for the excitation does not change for any given alternator.
Topics covered include:
- General electrical troubleshooting
- Four stroke diesel engine basics
- Engine control
- KW load sharing
- Alternator basics
- Alternator control
- KVA load sharing
- Synchronization
- Power triangle
- Panel meters and what they mean
- PWM operation
- Power limit
- Speed monitoring
- Ground fault
- Protective functions
- DC motor basics
- SCR operation (Device)
- IGBT operation (Device)
- Basic rectifiers
- Three phase rectifiers
- DC motor control
- Contactor logic
- System auxiliaries
- Dynamic Brake
- Two-motor control
- Shunt motor control
Siemens S7 PLC
Most PLC courses are programming courses. Most rig electricians have no need to do any programming. On rare occasions, it might be necessary to read a block or trace through a program, but in most cases, a service technician is called in to perform this task. A rig electrician needs to be able to troubleshoot the system that is controlled by the PLC.
WWPS realizes the above, and we have constructed our PLC class accordingly. Using our laptops and simulators, the students are shown how to work with the tools they are given, which are not standard programming tools. They are not given comments. They are not given symbol information. In short, they typically have an uploaded program that is fine for a computer, but that is nearly worthless for the technician or electrician.
We show the rig hand how to approach a system, and how to use the tools to find the problem so he can fix it using the abilities he already has. There is some preparatory work, but once our method is understood, the rig hand should be able to confidently approach any PLC-related system and troubleshoot it in a minimum amount of time.
The course contains both lecture and laboratory exercises. Students will need to demonstrate proficiency in a variety of tasks as well as pass a written test to receive a certificate. Retests can be taken for up to six months after the original class, if necessary.
Topics covered include:
- PLC basics
- Signal modules
- Field devices
- Typical circuits for field devices
- PLC configurations
- Indicators
- Communications
- System interconnections
- Block types and functions
- Digital basics
- Addressing
- Simatic manager S7
- Connecting to a PLC
- Communicating with a PLC
- Building VATs
- Adding comments
- Monitoring signals
- Symbol information
- Adding symbol information
- Exporting symbols and addresses
- Cross references
- Correcting mistakes (not programming)
- Filtering cross references
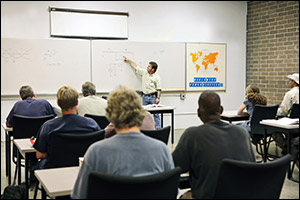